Materials
About
Materials research can be broken down into eight sub-areas:
- Ultrafinegrained Materials
- High Temperature Plasticity
- Fundamentals of Fatigue
- Polymer Composites
- Creep
- Mechanisms of Creep Plasticity
- Intermediate Temperature Creep and Fracture of Zircaloy
- Micromechanisms of Deformation
- “New X-Ray Microbeam Answers 20-Year-Old Metals Question” in the NIST Tech Beat describes fine scale stress measurements in a deformed metal. NIST web site.
- “Uncovering Secrets of the Strength of Materials” from Argonne National Lab’s web site.
- Thin Films
- Nanomechanics
Faculty
Wen Chen
Yong Chen
Andrea Hodge
Terence Langdon
Neda Maghsoodi
Paul Plucinsky
Hangbo Zhao
Labs
Additive Manufacturing Lab
Materials Processing & Characterization Lab
Mechanical Properties Lab
Zhao Research Group
Ultrafinegrained Materials
Ultrafine-grained (UFG) materials have two major advantages over conventional coarse-grained materials:
(i) they have high strength through the Hall-Petch relationship;
(ii) they have a potential for exhibiting superplastic ductilities at high temperatures.
There are two major procedures for producing metals with UFG structures:
Processing by ECAP is well developed at USC. We have a 150 ton Dake hydraulic press and several dies of different sizes and different angles (e.g. 90° and 110°). We are able to perform ECAP on samples having different diameters and over a range of pressing strain rates. We can also press samples at elevated temperatures. Numerous materials have been pressed using the facilities at USC. Although the emphasis has been on aluminum-based alloys, we have also pressed other materials such as magnesium alloys, copper alloys, pure iron and the Zn-22% Al eutectoid alloy.
Examples of the Application of ECAP to an Aluminum Alloy:
(i) Homogeneity through the cross-section of the sample after ECAP:
The structure becomes homogeneous with increasing number of passes and at the same time the hardness increases.
(ii) The break-up of precipitates in ECAP:
(iii) Very high elongations achieved after ECAP:
Superplastic elongations of >1000% are achieved in a spray-cast 7034 aluminum alloy after ECAP at a temperature of 473 K through either 6 passes (6p) or 8 passes (8p): the maximum elongation is displaced to faster strain rates when the number of passes is increased.
Reference: C. Xu, M. Furukawa, Z. Horita and T.G. Langdon, Acta Mater. 51, 6139 (2003).
Fundamentals of Fatigue
Mechanisms of Cyclic Plastic Deformation in Metals
M.E. Kassner, University of Southern California, DMR-0090080
Transmission electron micrograph (TEM) of dislocations in fatigued copper. Classic channels are bounded by dislocation dipole bundles. Locations are indicated where convergent beam electron diffraction (CBED) was used to determine the lattice parameter in order to assess any internal stress. The corresponding absence of residual stress with varying positions in the channels suggests that the Bauschinger effect, the basic element of metal fatigue, is understood in new terms. An Orowan mechanism (backstresses unimportant) appears to be a more reasonable approach to understand fatigue. This conclusion is consistent with earlier in-situ cyclic deformation experiments sponsored by NSF in the high voltage electron microscope. Metal fatigue is responsible for most structural failures.
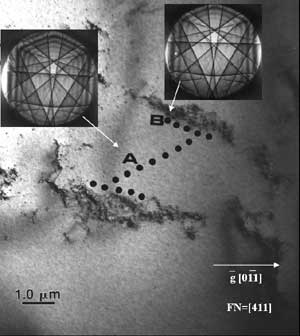
TEM micrograph of dislocations in fatigued copper. Classic channels are bounded by dipole bundles. Locations are indicated where convergent beam electron diffraction (CBED) was used to assess any internal stress. Taken by Dr. Maria Teresa Perez-Prado (post-doctoral researcher).
Publications
M.E. Kassner, M.-T. Pérez-Prado, K.S. Vecchio, and M.A. Wall, “Determination of Internal Stresses in Cyclically Deformed Cu Single Crystals Using CBED and Dislocation Dipole Separation Measurements,” Acta Materialia, 48, pp. 4247-4254, 2000.
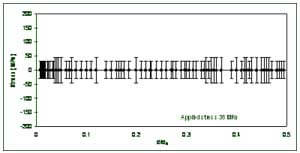
The corresponding absence of residual stress with varying positions in the fatigue-structure channels suggests that the Bauschinger effect, the basic element of metal fatigue, is understood in new terms.
Creep
Mechanisms of Creep Plasticity
This research examines the basic mechanisms of time-dependent plasticity at elevated temperatures. Specifically, this research will assess the importance of dislocation heterogeneities (e.g. subgrain boundaries) on the mechanism of creep. Internal or “back” stress measurements are performed using convergent beam electron diffraction (CBED) measurements [at UCSD]. Anealasticity, possibly in association with internal backstresses, will be studied. Finally, fundamental relationships will be formulated to describe creep plasticity. Funding provided by Basic Energy Sciences of the Dept. of Energy.
Publications
Taylor hardening in five-power-law creep of metals and Class M alloys
Intermediate Temperature Creep and Fracture of Zircaloy
This work examines the mechanisms of creep plasticity and, especially, fracture at the intermediate temperatures that are relevant to interim dry storage of nuclear waste. Work will examine whether the mechanism of creep fracture is cavitation related. The details of creep plasticity especially as relevant to glide and climb- controlled processes are researched. Funding provided by Lawrence Livermore National Laboratory and Sigma Xi.
Publications
Steady-State Creep of a-Zirconium at Temperatures up to 850 C